Solutions for Composites
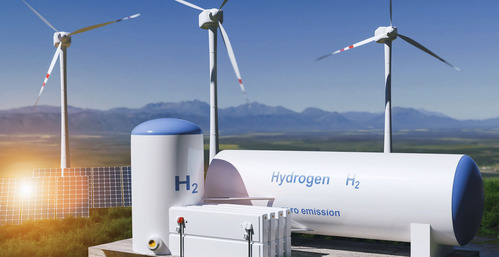
Solutions for Composites
For the past 75 years, SAHM has been a technical innovation leader in winding - with more than 350,000 winders delivered for all kinds of applications. SAHM has solutions for PAN, rayon and pitch precursors, as well as carbon and pre-impregnated fibers (prepregs).
SAHM offers winding solutions
- for undirectional prepregs,
- with solvent or hot melt termoset polymers (epoxy),
- with thermoplastic polymers.
Composites prepared with SAHM winders are used in a broad array of high-tech applications and industries:
- Aerospace
- Automotive
- Wind power
- Filament winding
- Pressure vessels
- Civil engineering
- Sports equipment
Together with our partners, we can deliver complete solutions and turnkey projects. We are ready to provide everything needed for:
- Precursor and carbon fiber production
- Undirectional filament impregnation
- Tow-preg lines
- One side / double side binder applications
- UD-prepreg slitting, winding and rewinding
Tow-preg winding solutions
Inline tow-preg production is becoming more and more popular as it helps to reduce costs. The process starts by directly coating single carbon fiber tows, then fixing the width, and finally rewinding the impregnated material back onto bobbins. The unidirectional towpregs are then used at the Automatic Fiber Placement Systems (AFP) or Filament Winding Machines.
The wide range of impregnation methods and various types of chemicals – from hot melt to solvent dip and warm-preg dipping – make it necessary to have programmable winders that handle the different types of impregnated tows. With their proven flexibility, SAHM winders deliver optimum package build up and stability. This is a key point for successful unwinding and further processing of the impregnated material.
The different materials used for thermoset and other thermoplastic polymers display varying degrees of adhesion – which affects unwinding dynamics. Sticky or wet prepregs need lots of unwinding tension applied during unreeling. This, however, can cause processing difficulties and fiber damage. To avoid this problem, it is necessary to wind a softer bobbin – adjusting to achieve optimum tension, bail pressure and winding ratio, which then fits precisely to the width and characteristics of the impregnated tow.
By contrast, when the prepreg is dry, winding a soft bobbin would make the package unstable and in some cases unusable. Whatever the specific winding situation, optimizing winding parameters will increase the efficiency of the subsequent processes.
- For example, a downstream filament winding machine can then run at faster speeds for more cost effective production.
- It also helps to avoid waste by eliminating scrap involving impregnated spools that cannot be properly unwound/unrolled or scrap caused by packages falling apart at the bobbin edge.
With our long experience and proven expertise in winding, unwinding and rewinding, the electronically programmable SAHM winders ensure optimum and reproducible winding quality for towpregs made from carbon, glass or aramid fibers.
Areas of application: Automotive, Aerospace, Wind Power, Sporting Goods and many others.
Slit-tow winding solutions
Conventional unidirectional (UD) prepregs are produced in a hot-melt process. This involves laying out dry untreated fibers strands next to each other which are then covered on both sides with a layer of resin. The application of pressure then creates a foil-like sheet of material, which is finally slit into thin tapes.
The slit tapes produced in this way (so-called thermoset slit tapes) are precisely dimensioned and can be wound with or without lamination tape for easy unrolling. They are frequently used for further production steps, particularly for non serially produced parts.
The processing advantages of slit tapes may come with some drawbacks. Slit tapes have a short period of possible use and there are difficulties associated with the necessity of low-temperature storage and sensitivity of spools during transport and logistics, which often result in waste. This can become a significant cost factor, especially in connection with transport and import regulations for foreign shipment.
Together with other German technology companies, SAHM offers systems that enable slitting and spooling of slit tows in-house for just-in-time production. This saves time and provides fresh, high quality material for production, eliminating the high costs associated with transport and storage of these sensitive materials. The SAHM in-house production systems also allow greater independence and flexibility in production – whatever the scale of manufacturing may be.
In contrast to traditional tow guiding methods, slit materials with their high-precision requirements are best wound by moving the spool itself. Thanks to SAHM’s programmable winding options with a single machine, it is possible to wind up various spool shapes and sizes – cylindrical, with angled sides or as so-called pancakes with or without flanges.
The full integrity and suitability of the produced packages for downstream production processes can only be ensured through a determination and application of the correct winding parameters, such as tension, bail pressure, optimum winding angle and spacing, combined with independent tension control of the newly inserted liner.
The inserted slit-tow separation film is usually thinner and slightly wider than the slit tow itself. Production of a stable spool is therefore only possible when the unwinding and winding parameters of both materials settings are in precise agreement. With SAHM winders, the wide range of settings for optimizing winding parameters is also supported by storage and recall capabilities for the saved recipes for each material type and each slit width. This ensures reproducible quality and user-friendly handling of many different recipes.
Area of application: Aerospace
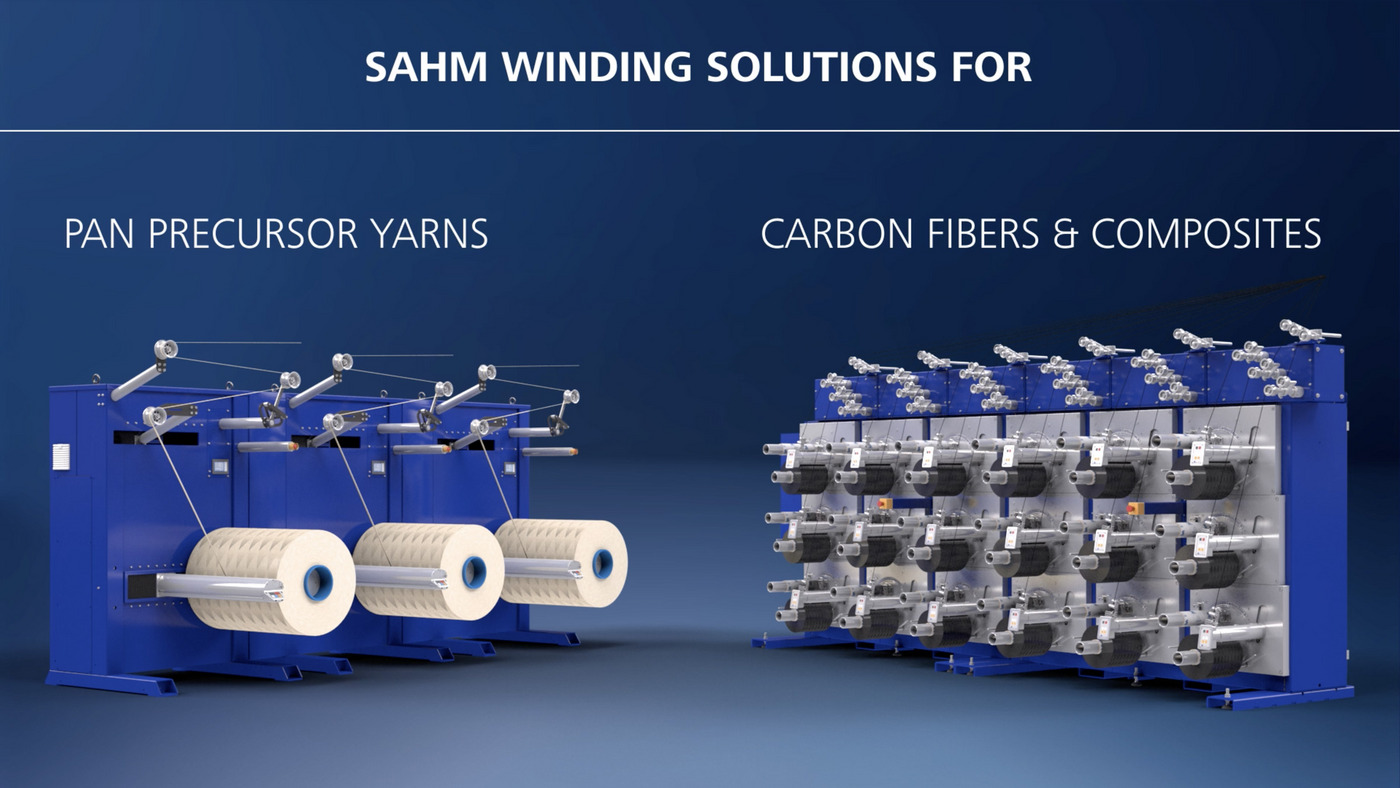
SAHM 872XE
SAHM 460XE Series
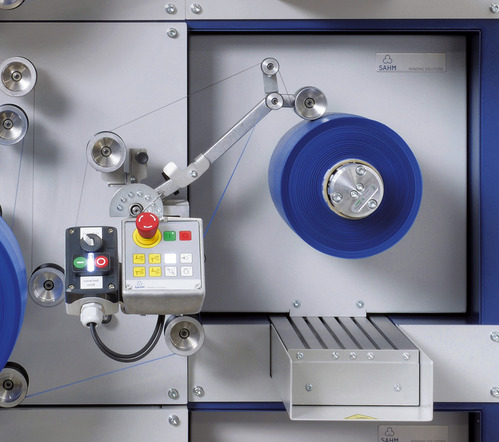
SAHM 460XE Series
These precision parallel winding machines with traversing spindle are specially designed to meet the demanding requirements that come with handling sensitive materials and tapes.
The winders of the SAHM 460XE series produce bobbins of consistently high quality and support a multitude of bobbin types and winding materials. Their low maintenance design ensures reliable and highly predictable machine availability.
CarbonStar 2-cop
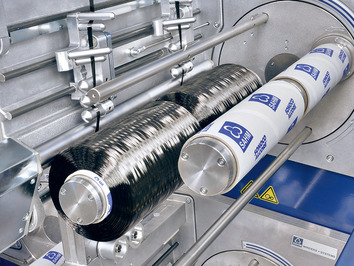
CarbonStar 2-cop
Combination of all maximum values is not possible
- Applications
- Carbon fibers
- Specific towpregs
- Advantages
- Maximum efficiency by production of two bobbins (each up to 20 kg) on one winding head
- Two exact length, high quality spools with our patented diameter control
- Bobbin change-over reliability of 99.8 %
- Highest operating safety due to automatic change-over
- Energy savings from the latest drive technology
- Minimum space requirement
- Very low maintenance costs
- Zero production waste - no downtime during bobbin changeover
- Metered yarn length
- Technical dataTiter3 to 60 K*Winding speed2 to 20 m/minTraverse length2 x 250 mmDriveFrequency-controlledFrame1-, 2- or 3-tierTube inside diameter76.2 mmTube length280 mmWinding ratioElectronicPackage weightUp to 20 kg each bobbinYarn tensionElectronically adjustablePackage diameterMax. 320 mmWinding technologyPrecision cross winding*others on request.
Combination of all maximum values is not possible - Features
- Automatic bobbin changeover on reaching one of the following criteria: yarn length, winding time, package weight, package diameter or external signal
- Quick and efficient product changes by electronic data input of all winding parameters
- Electronically controlled winding ratio
- Central process control unit (HMI 12" touch screen) for input, display and storage of process and machine parameters
- Tube inside diameter (76.2 mm) tolerance + 0.5 mm possible
- Options
- HMI 15" touch screen with high capacity processor for SQL database
- Interface to DCS
- Frame unit with 9 heads
- Label printing system
- Carbon fibers
- Specific towpregs
CarbonStar II - big
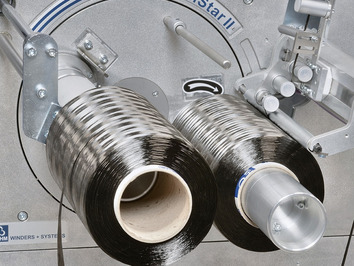
CarbonStar II - big
Combination of all maximum values is not possible
- Applications
- Carbon Fibers
- Specific Towpregs
- Advantages
- Quick and efficient product changes
- Zero production waste - no downtime during bobbin changeover
- Metered yarn length
- Bobbin changeover reliability of 99.8 %
- Highest operating safety - yarn is caught and cut at rear of bobbin
- Minimum yarn tail after automatic changeover
- Technical dataTiter12 to 60 K*Winding speed2 to 15 m/minTraverse lengthMax. 250 mmFrame3-tierTube inside diameter76.2 mmTube length280 mmWinding ratioElectronicPackage weightUp to 20 kgYarn tensionElectronically adjustablePackage diameterMax. 320 mmWinding technologyPrecision cross windingBobbin mandrelPneumaticalParking position with push off deviceIncluded*others on request.
Combination of all maximum values is not possible - Features
- Automatic bobbin changeover on reaching one of the following criteria: yarn length, winding time, package weight, package diameter or external signal
- Quick and efficient product changes by electronic data input of all winding parameters
- Electronically controlled winding ratio
- Central process control unit (HMI touch screen) for input, display and storage of process and machine parameters
- Tube inside diameter (76.2 mm) tolerance + 0.5 mm possible
- Options
- Variable traverse lengths
- HMI touch screen with high capacity processor for SQL database
- Interface to DCS
- Adaptable to an automatic bobbin handling system
- Frame unit with 6 heads
- Label printing system
- Carbon Fibers
- Specific Towpregs
CarbonStar II - standard
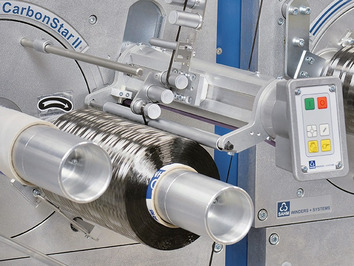
CarbonStar II - standard
Combination of all maximum values is not possible
- Applications
- Carbon Fibers
- Specific Towpregs
- Advantages
- Quick and efficient product changes
- Zero production waste - no downtime during bobbin changeover
- Metered yarn length
- Bobbin changeover reliability of 99.8 %
- Highest operating safety - yarn is caught and cut at rear of bobbin
- Minimum yarn tail after automatic changeover
- Technical dataTiter3 to 60 K*Winding speed2 to 15 m/minTraverse lengthMax. 250 mmFrame3-tierTube inside diameter76.2 mmTube length280 mmWinding ratioElectronicPackage weightUp to 12 kgYarn tensionElectronically adjustablePackage diameterMax. 250 mmWinding technologyPrecision cross windingBobbin mandrelPneumaticalParking position with push off deviceNot included (option available)*others on request.
Combination of all maximum values is not possible - Features
- Automatic bobbin changeover on reaching one of the following criteria: yarn length, winding time, package weight, package diameter or external signal
- Quick and efficient product changes by electronic data input of all winding parameters
- Electronically controlled winding ratio
- Central process control unit (HMI touch screen) for input, display and storage of process and machine parameters
- Tube inside diameter (76.2 mm) tolerance + 0.5 mm possible
- Options
- Variable traverse lengths
- HMI touch screen with high capacity processor for SQL database
- Interface to DCS
- Adaptable to an automatic bobbin handling system
- Frame unit with 6 heads
- Label printing system
- Carbon Fibers
- Specific Towpregs
SAHM 880XE
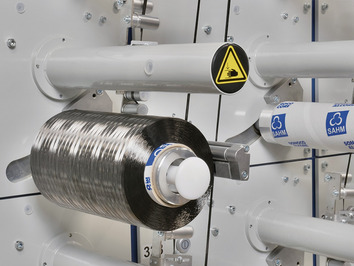
SAHM 880XE
Combination of all maximum values is not possible
- Applications
- Carbon fibers
- Specific towpregs
- Advantages
- Excellent package quality
- Quick and efficient product changes
- Electronic input of all winding parameters
- Compact and modular design
- Reproducible yarn package formation
- Technical dataTiter1 to 60 K*Winding speed1 to 15 m/minTraverse lengthMax. 250 mmDriveFrequency-controlledFrame4-tierTube inside diameter76.2 mmTube length280/290 mmWinding ratioElectronicYarn tensionElectronically adjustablePackage diameterMax. 250 mmWinding technologyPrecision cross winding*others on request.
Combination of all maximum values is not possible - Features
- Electronically controlled and infinitely variable winding ratio
- Central Process Control Unit (HMI 12" touch screen) for input, display and storage of process and machine parameters
- Possible speed synchronization with the preceeding process
- Doffing timer function
- Advanced tension control with strain gauge system (yarn guide roller with implemented tension sensor)
- Options
- Pneumatic mandrel
- Variable traverse lengths
- HMI 15" touch screen with high capacity processor for SQL database
- Label printing system
- Carbon fibers
- Specific towpregs