Single end extrusion coating line
YarnStar 3+ - Coating - Cooling - Winding+Automation
The YarnStar 3+ is a mono and bicolor single end extrusion coating line designed for a high degree of flexibility and a broad application range.
The extremely compact line coats single ends of textile and technical yarns in excellent coated yarn quality. The integrated line concept of the YarnStar 3+ achieves production speeds up to 1,500 m/min.
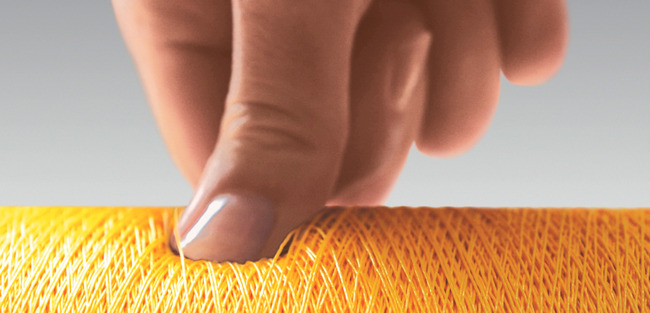
Fewer cross marks due to soft winding
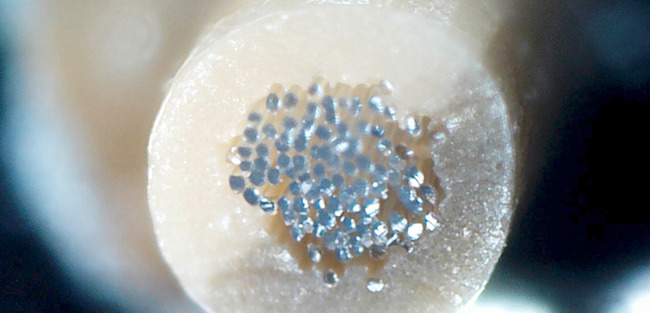
Exact core yarn centricity
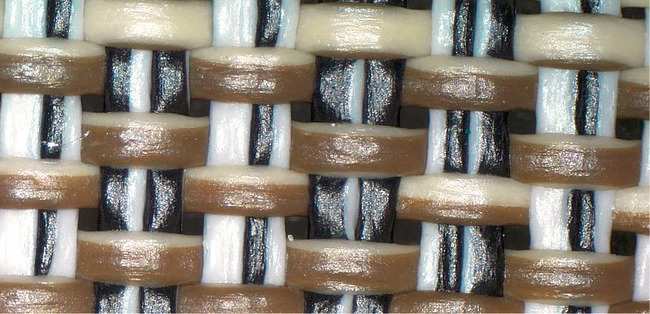
Bicolor fabric
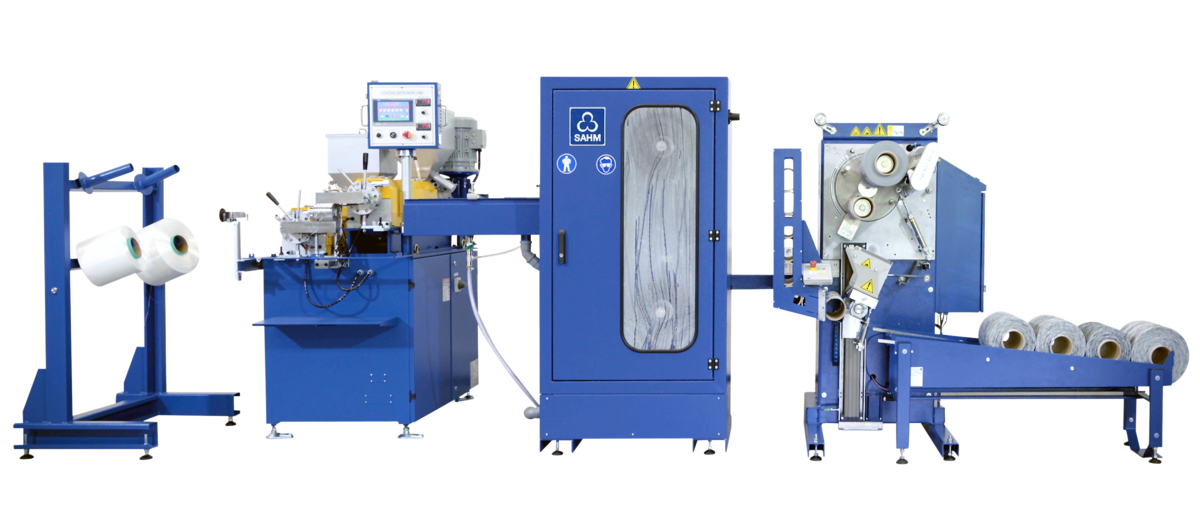
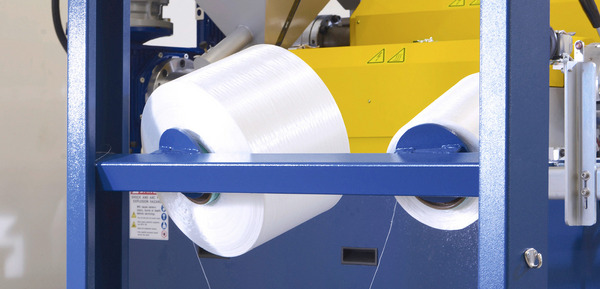
Unwinding creel for polyester feed packages
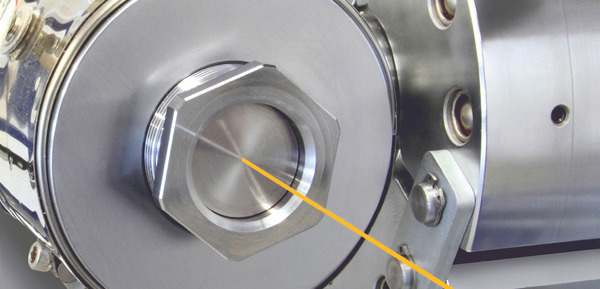
Screw extruder with 5 heating zones
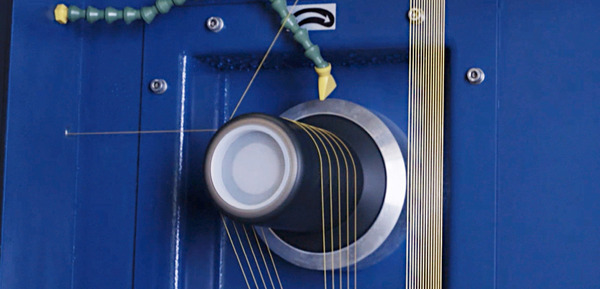
Chill unit
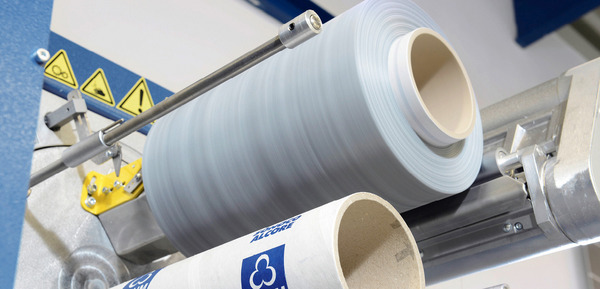
Automatic precision winding and bobbin change
The finished package is transported to a storage unit which is emptied from time to time by the operator.
Your advantages
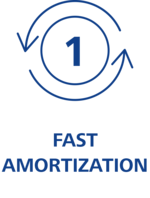
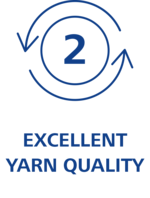
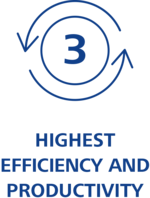
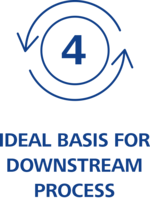
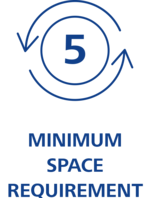
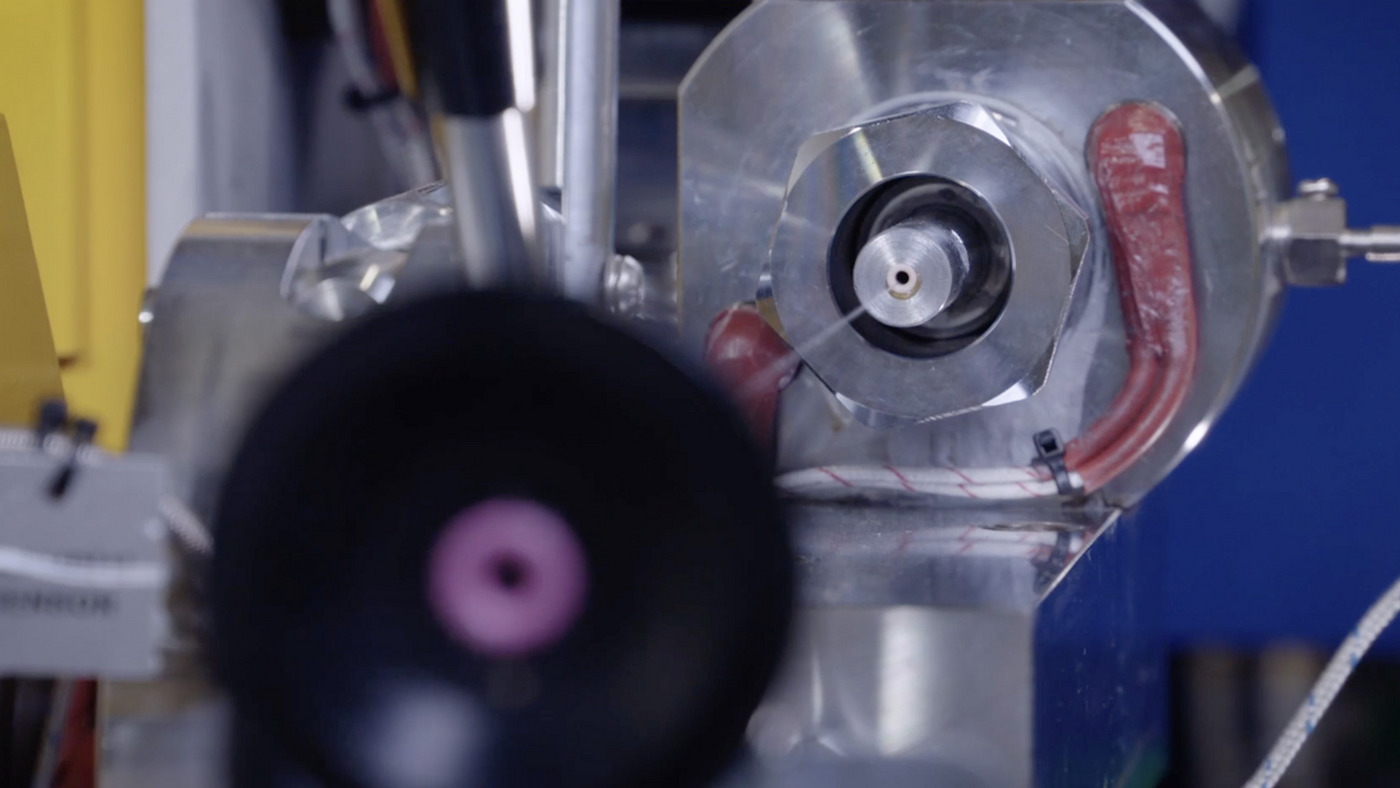